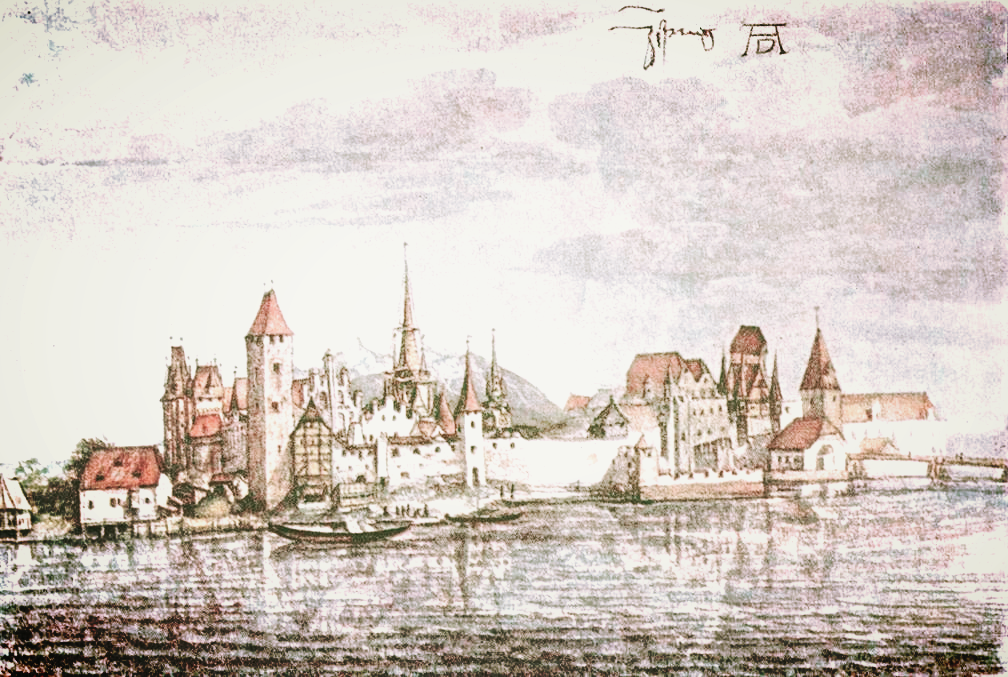
An Introduction to Norse Glass Beads with focus on Hedeby
By Mayken van der Alst
A 10th century Arab once said that the Vikings would "go to any length to get hold of colored beads" (Wernick, 94). Judging by the number of beads as grave goods in female burials and stray finds in settlement excavations it becomes obvious that glass beads were a much coveted and integral part of the female Norse dress.. Beads were only found in small numbers in male graves indicating their use as amulets instead of jewelry. Glass beads also played an important role in trade and as a substitute for coinage. Along with hack silver and coins they can be found in many hoards. Imported glass beads reveal trade routes for example carnelian and silver beads imported from India and Iran via Islamic and Rus traders or even colored glass beads from Birka. Beads were made from a variety of materials such as glass, silver, gold, amber and jet as well as a wide range of semi-precious gemstones.
The earliest traces of Scandinavian glass production date to the 6th and 7th century and were discovered in Gotland. Glass production seemed to have rooted in central Scandinavia from the 8th century onwards with centers such as Ahus, Ribe, Birka, Kaupang and Hedeby. While at first researchers assumed that Norse only traded with beads excavations at Birka and Hedeby have shown that there was indeed a glass making industry that produced items from wound or blown glass such as beads, rings, vessels, game pieces, etc.
Colors and Designs
While many shapes and color combinations were possible to achieve then as they are now the majority of glass beads excavated at Viking sites were not all that fancy. The simple flattened round or disk-shaped single-colored bead makes for about 77% of the over seven thousand beads found in Hedeby for example. Blue is the most common color with 38% followed by green (25%) , and yellow (18%) with white, grey blue, red, clear and others never claiming more than 6%. The common Norse bead is rather small and measures between 3.5mm and 6.5mm.
Typical decoration of glass beads include zigzag lines, eyes, figure 8, dots, straight lines, spiral patterns, herringbone or feather patterns. Millefiori in its simpler forms was fairly popular with a basic flower shape, eyes and chessboard patterns the most common forms.
Definitions
Glass beads are made in three basic ways: wound, pierced, and cut.
Wound bead: The glass is heated and then wound onto a prepared mandrel.
Pierced Bead: The molten glass is shaped to a bead form and then pierced with a metal rod in order to make the hole.
Cut bead: Glass tubing is heated and then stretched to obtain the desired thickness
of the bead. The Tubing is then cut with glass cutters to obtain the individual beads
Stringer: A thin rod of glass which can then be used to add decorative details to beads.
Bead release: A semi-liquid clay used to cover the mandrel to prevent the molten glass sticking to the metal.
Basic Safety Rules
- Set up your lampworking work space in a well ventilated area
- Remove all flammable items from and from around your work area
- Wear close-fitted clothing from natural fiber
- Wear safety glasses
Step-by-step method of producing wound glass beads:
1. Prepare the mandrels. The mandrels must be coated in bead separator to prevent the bead from sticking to the mandrel.
2. Prepare the work area.
3. Heat the glass. The glass is passed in and out of the flame to heat it slowly until its color starts to change. Once the glass is warm it is then heated up in the flame until a round ball of molten glass is formed.
5. Form a bead. Once a round ball of molten glass forms on the end of the rod, touch the glass to the prepared mandrel and roll the mandrel between your fingertips away from you. Continue to turn your mandrel in the heat until you have the desired amount of glass on the mandrel then wind off the glass from the rod. Winding off is accomplished by slowly pulling the glass rod away from the bead and then burning off the stringer that connects the bead and the glass rod. Next keep the bead in the heat and continue turning the mandrel until the bead is round.
6. Decorate and form the Bead. Once you have a basic round bead the bead can be decorated with stringers or formed using tools.
7. Anneal the Bead. Once the bead is formed and decorated it must be annealed in order to keep the bead from cracking. Small beads can be slowly cooled down in a Vermiculite blanket; larger beads need to be annealed in a bead annealing kiln. In period the beads were placed on the edge of the furnace or kiln. The beads were left at the edge of the furnace or kiln throughout the bead making session annealing the beads as the bead maker worked.



It happens to the best of us - Viking age bead stuck on mandrel